울산조선해양플랜트기자재사업협동조합 조합원사
레이저가공 사업장 3월 가동…조선업 공정 스마트화 촉진
안전사고⋅날림먼지 방지… 정밀⋅신속가공으로 효율 높여
김대환 대표 “IT 접목해 수작업 따른 고질적 인력난 해소”
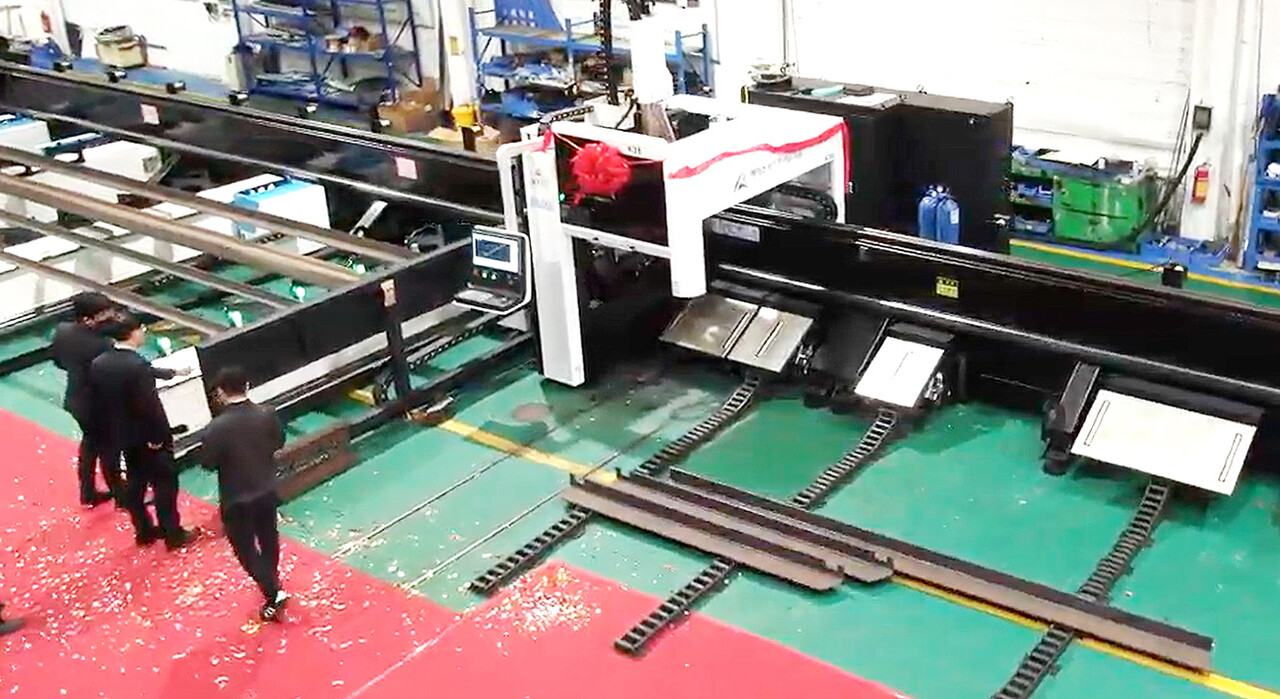
울산에 소재한 중소기업협동조합원사인 한 중소기업이 선박 건조에 사용되는 형강을 수작업 대신 자동으로 절단하는 기술과 설비를 도입한다. 조선업 뿌리기술로 분류되는 이 작업에 자동화 공정을 전격 적용한 것이다.
이에 따라 형강 절단 효율과 제품 품질을 개선할 뿐만 아니라, 조선업 전반으로 스마트 공정 도입을 촉진하는 효과도 기대된다.
조선해양·플랜트 엔지니어링 IT 기업인 에이스이앤티는 울산시 울주군 서생 에너지융합산업단지에 ‘레이저 가공 기술 사업장’을 최근 준공하고, 3월 가동을 앞두고 있다. 에이스이앤티는 울산조선해양플랜트기자재사업협동조합의 회원사로 활동하고 있다.
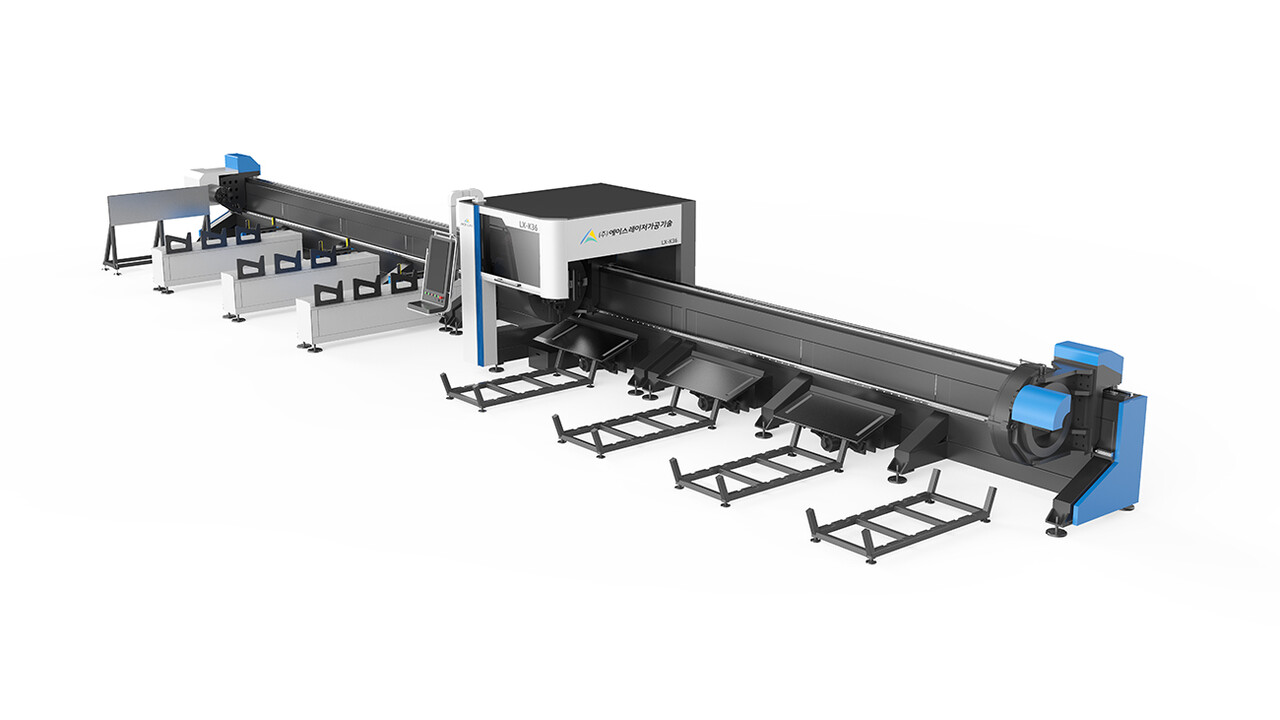
조선업 스마트 제조 혁신을 목표로 구축되는 이 사업장에는 레이저를 이용해 형강을 자동으로 절단하는 장비가 들어선다.
형강은 ㄱ·H·T 등 단면 모양이 다양한 철강재로, 선박 블록을 만들 때 뼈대 역할을 하는 자재다. 현재 수십m에 달하는 형강을 절단할 때는 현장 야드에서 수작업으로 산소 절단하거나, 일부 플라스마 기체를 활용한 반자동 가공 방식이 사용된다.
이런 방식으로는 작업에 오차가 생기거나 재료 소모량이 늘어나는 등 효율이 떨어질 수 있다. 안전사고나 날림먼지를 비롯한 환경 문제 우려도 있다. 에이스이앤티가 도입한 장비는 일련의 작업 과정을 모두 자동으로 처리한다. 작업 효율을 높이는 동시에 안전과 환경 문제도 해결할 수 있다는 게 업체 측 설명이다.
이 장비는 길이 45.7m, 너비 4.2m, 높이 3.5m 규모다. 가공이 필요한 형강을 올리고 내리는 ‘로딩’과 ‘언로딩’ 부분이 각각 20m, 형강을 잡아주는 역할을 하는 ‘척’(chuck)의 최대 지름이 35㎝에 달한다. 이 장비를 활용하면 두께가 5㎝에 달하는 두꺼운 형강도 정밀하고 신속하게 절단할 수 있다.
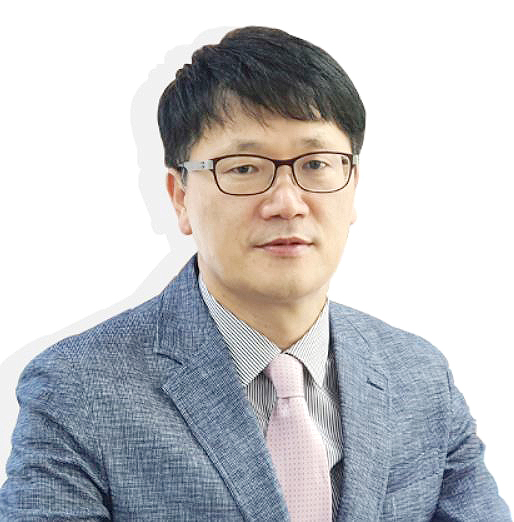
김대환 에이스이앤티 대표(사진)는 “기존 산소 절단 방식으로 인력 10명이 붙어서 1개월가량 걸리는 작업 물량을, 레이저 절단 장비로는 4~5명이 1주일 만에 끝낼 수 있을 것”이라고 했다.
김 대표는 이어 “최근 심각해진 조선업 인력난에 대응하는 동시에, 젊은 청년 인력들이 IT를 접목해 작업을 스마트화하는 효과도 거둘 것으로 본다”고 덧붙였다.
이 회사는 인공지능(AI)을 접목한 물류 자동화 등 조선업 분야 지능형 공장 구축을 위해 세계적인 디지털 비즈니스 플랫폼 기업과 협력에도 나선다.
이를 통해 레이저 가공 자동화 공정 기술력을 강화하고, 나아가 울산 조선·플랜트 산업 역량을 높이도록 시너지를 낸다는 방침이다.
김 대표는 “IT와 디지털을 적용해 조선업을 혁신한다는 선언이 나온 지 수년이 지났지만, 크고 무거운 강재를 다루는 산업이다 보니 스마트화 속도가 더딘 측면이 있었다”고 지적했다. 그는 “조선업의 시작점이라 할 수 있는 형강 절단 작업이 자동화하면, 선박 블록 조립 등 후속 공정 전반에도 자동화를 촉진하는 긍정적인 효과가 있을 것”이라며 “조선산업의 고질적인 인력난 해소도 기대가 된다”고 설명했다.